Get Fast and Efficient Packaging Machine Repair for Your Production Line
Get Fast and Efficient Packaging Machine Repair for Your Production Line
Blog Article
The Ultimate Overview to Product Packaging Device Repair Work: Maintain Your Procedures Running Efficiently
In the world of packaging, the efficiency of operations pivots substantially on the dependability of machinery. Comprehending the complexities of product packaging equipment repair work is vital for maintaining ideal performance and reducing disturbances. Regular upkeep not just prolongs the life of these machines yet additionally addresses common problems that can hinder productivity. As we explore the nuances of troubleshooting and the critical decision-making process between repair and substitute, it ends up being clear that a positive approach can yield considerable benefits. What particular strategies can companies apply to guarantee their packaging operations stay undisturbed?
Importance of Normal Maintenance
Regular maintenance of packaging makers is vital for making sure optimal efficiency and long life. By applying a structured upkeep schedule, operators can determine possible problems prior to they intensify right into significant issues. This proactive method not only decreases downtime however also extends the life expectancy of the equipment, ultimately resulting in decreased functional expenses.
Routine evaluations permit the evaluation of critical elements such as belts, sensing units, and seals. Addressing damage without delay protects against unexpected failures that can interrupt manufacturing and cause pricey repair work. Furthermore, routine upkeep assists ensure conformity with industry criteria and guidelines, promoting a safe workplace.
In addition, maintenance activities such as cleansing, lubrication, and calibration significantly improve machine effectiveness. Boosted performance translates to constant product quality, which is crucial for preserving client satisfaction and brand reputation. A well-maintained product packaging device operates at ideal rates and reduces material waste, adding to general performance.
Typical Packaging Equipment Problems
Packaging machines, like any complicated machinery, can run into a selection of common issues that might prevent their performance and performance - packaging machine repair. One common trouble is inconsistent sealing, which can bring about product spoilage and waste if packages are not properly secured. This usually arises from misaligned components or used sealing elements
One more constant problem is mechanical jams, which can happen because of international things, worn parts, or incorrect positioning. Jams can trigger delays in production and increase downtime, inevitably impacting overall productivity. In addition, digital breakdowns, such as failing in sensing units or control systems, can lead and interrupt operations to incorrect measurements or unpredictable machine habits.
Moreover, problems with item feed can also emerge, where things may not be delivered to the product packaging location continually, causing disturbances. Wear and tear on belts and rollers can lead to suboptimal efficiency, needing immediate interest to prevent more damage.
Understanding these usual issues is crucial for keeping the stability of product packaging operations, guaranteeing that equipment runs smoothly and successfully, which subsequently assists in meeting manufacturing targets and keeping product high quality.
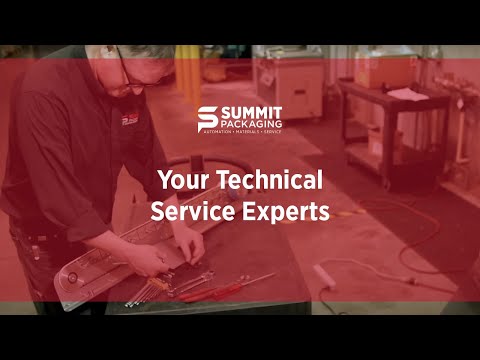
Fixing Techniques
Efficient repairing strategies are crucial for quickly resolving issues that develop view it with product packaging devices. An organized technique is important for determining the origin of breakdowns and decreasing downtime. Begin by gathering details about the signs observed; this might consist of unusual noises, functional hold-ups, or mistake codes presented on the machine's interface.
Following, describe the machine's manual for fixing guidelines particular to the version concerned. This source can provide beneficial understandings right into common concerns and advised analysis steps. Use aesthetic evaluations to inspect for loosened connections, worn belts, or misaligned components, as these physical aspects commonly add to functional failings.
Carry out a procedure of elimination by screening individual maker features. If a seal is not forming properly, analyze the securing system and temperature level setups to figure out if they satisfy functional specs. Document each step taken and the results observed, as this can assist in future troubleshooting efforts.
Repair vs. Substitute Decisions
When confronted with devices breakdowns, choosing whether to replace a product packaging or fix device can be a facility and vital selection. This choice pivots on a number of crucial aspects, consisting of the age of the equipment, the extent of the damages, and the forecasted effect on operational efficiency.
First of all, think about the maker's age. Older equipments might need more constant repairs, leading to higher collective costs that can go beyond the financial investment in a brand-new device.
Operational downtime is another vital consideration. If fixing the machine will create long term hold-ups, purchasing a new maker that supplies improved effectiveness and dependability may be more prudent. Additionally, think about the schedule of parts; if substitute parts are tough to find by, it may be a lot more strategic to replace the device entirely.
Inevitably, carrying out a cost-benefit analysis that includes both long-lasting and prompt ramifications will assist in making a notified decision that straightens with your functional goals and monetary constraints. (packaging machine repair)
Safety Nets for Longevity

Trick safety nets consist of routine lubrication of moving parts, placement checks, and calibration of controls and sensing units. Developing a cleaning schedule to remove debris and impurities from machinery can dramatically reduce damage (packaging machine repair). Furthermore, checking functional criteria such as temperature level and resonance can aid identify irregularities early
Training staff to recognize signs of wear or malfunction is another important element of precautionary upkeep. Encouraging operators with the understanding to carry out fundamental troubleshooting can cause quicker resolutions and decrease functional disturbances.
Documents of maintenance tasks, including service records and inspection findings, fosters liability and assists in informed decision-making relating to repairs and substitutes. By focusing on safety nets, companies can ensure their product packaging makers operate at peak efficiency, eventually resulting in raised productivity and minimized operational expenses.
Conclusion
To conclude, the reliable repair and maintenance of packaging machines are vital for maintaining operational performance. Normal maintenance minimizes the risk of usual problems, such as irregular sealing and mechanical jams, while methodical troubleshooting methods facilitate prompt resolution of malfunctions. Mindful factor to consider of repair service versus substitute decisions contributes to cost-effective monitoring of resources. By executing preventive steps, businesses can why not try these out improve equipment long life and make certain uninterrupted efficiency in product packaging procedures.
Comprehending the details of product packaging equipment repair is crucial for keeping optimum efficiency and minimizing interruptions.Normal upkeep of product packaging makers is vital for making certain optimal efficiency and durability.Product packaging equipments, like any complex equipment, can come across a selection of typical problems that may hinder their performance and efficiency. If repairing the maker will cause extended delays, investing in a new machine that offers enhanced performance and integrity may be a lot more prudent.In conclusion, the efficient upkeep and fixing of packaging equipments are extremely important for sustaining operational efficiency.
Report this page